Products
- Products
- Categories
- Blog
- Podcast
- Application
- Document
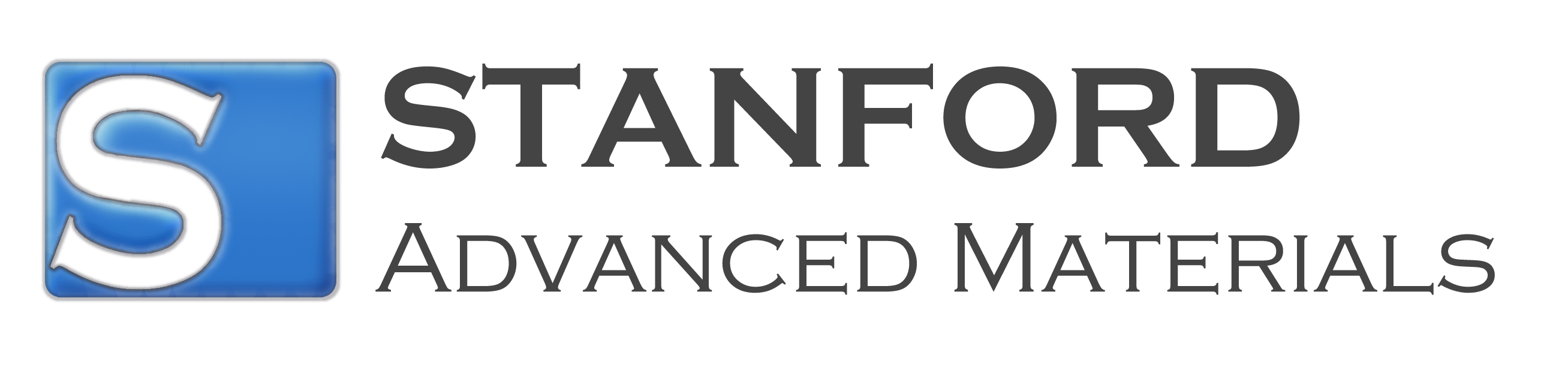
PRODUCT
Precious MetalsExotic MetalsAluminumAntimonyBariumBerylliumBismuthCadmiumCalciumCeriumChromiumCobaltCopperDysprosiumErbiumEuropiumGadoliniumGalliumGermaniumGoldHafniumHolmiumIndiumIridiumIronLanthanumLeadLithiumLutetiumMagnesiumManganeseMolybdenumNeodymiumNiobiumNickelPalladiumPlatinumPotassiumPraseodymiumRheniumRhodiumRubidiumRutheniumSamariumScandiumSilverSodiumTantalumTerbiumThuliumTinTitaniumTungstenVanadiumYtterbiumYttriumZincZirconium
INDUSTRIES
Chemical & Pharmacy Pharmaceutical Industry Aerospace Agriculture Automotive Chemical Manufacturing Defense Dentistry Electronics Energy Storage & Batteries Fuel Cells Investment Grade Metals Jewelry & Fashion Lighting Medical Devices Nuclear Energy Oil & Gas Optics Paper & Pulp Pharmaceuticals & Cosmetics Plating Research & Laboratory Solar Energy Space Steel & Alloy Producers Sports Equipment Textiles & Fabrics
APPLICATIONS
Tungsten Applications Metallurgy Semiconductor Rare-earth Magnets Catalyst 3D Printing Powder High Entropy Alloy Powder Metal Injection Molding Additive Manufacturing Thermal Spraying Coatings Hot Isostatic Pressing Rare Earth Element Application Environmental Catalysts Marker Band OLED Materials Thermocouple Wire Packing & Internals Li-ion Battery & Electronic Chemicals Metal Powders for Diamond Tools Soft Magnetic Powder
GET A QUOTE
English
Española
Deutsch
Français
Italiano
/ en
Select Language





-
- Chemical & Pharmacy
- Pharmaceutical Industry
- Aerospace
- Agriculture
- Automotive
- Chemical Manufacturing
- Defense
- Dentistry
- Electronics
- Energy Storage & Batteries
- Fuel Cells
- Investment Grade Metals
- Jewelry & Fashion
- Lighting
- Medical Devices
- Nuclear Energy
- Oil & Gas
- Optics
- Paper & Pulp
- Pharmaceuticals & Cosmetics
- Plating
- Research & Laboratory
- Solar Energy
- Space
- Steel & Alloy Producers
- Sports Equipment
- Textiles & Fabrics
-
- Tungsten Applications
- Metallurgy
- Semiconductor
- Rare-earth Magnets
- Catalyst
- 3D Printing Powder
- High Entropy Alloy Powder
- Metal Injection Molding
- Additive Manufacturing
- Thermal Spraying Coatings
- Hot Isostatic Pressing
- Rare Earth Element Application
- Environmental Catalysts
- Marker Band
- OLED Materials
- Thermocouple Wire
- Packing & Internals
- Li-ion Battery & Electronic Chemicals
- Metal Powders for Diamond Tools
- Soft Magnetic Powder