Additive Manufacturing vs Traditional Manufacturing
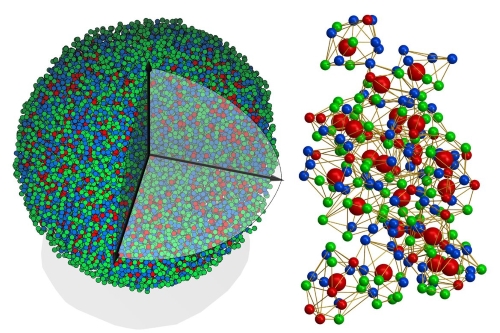
Join Eric Smith at Stanford Advanced Materials as he sits down with Dr. Laura Bennett, an expert in additive manufacturing, and Dr. John Taylor, a veteran in traditional manufacturing, to explore the strengths and challenges of these two production methods. Discover how additive manufacturing, with its design flexibility and waste reduction, is transforming industries like healthcare, while traditional methods continue to excel in mass production and efficiency.
The episode delves into the practical considerations of equipment and facility needs, and how hybrid approaches might shape the future of manufacturing. Whether you’re curious about 3D printing or the enduring power of traditional techniques, this discussion offers valuable insights into the technologies driving modern production.
Want to learn more? Send an inquiry or connect with us on social media.
Welcome to Stanford Advanced Materials! I’m Eric Smith, and today we’re exploring the fascinating world of manufacturing, focusing on the comparison between additive manufacturing, also known as 3D printing, and traditional manufacturing methods. To help us navigate this discussion, we have two experts with us: Dr. Laura Bennett, a specialist in additive manufacturing, and Dr. John Taylor, who brings years of experience in traditional manufacturing. Thank you both for joining us!
Thanks, Eric! Additive manufacturing is revolutionizing production, and I’m excited to dive into its advantages.
Likewise, Eric. Traditional manufacturing has been the backbone of industry for centuries, and it’s fascinating to see how new technologies like additive manufacturing are reshaping the landscape.
Let’s start with a basic overview. Laura, what exactly is additive manufacturing, and how does it differ from traditional methods?
Additive manufacturing is a process where objects are built layer by layer, using materials like plastics, metals, or ceramics. This is in contrast to traditional manufacturing, which is typically subtractive—meaning materials are cut, drilled, or machined away from a larger piece to create the final product. The layer-by-layer approach allows for incredible design flexibility, enabling the creation of complex geometries that are often impossible with traditional methods.
That’s a great point. Traditional manufacturing is often limited by the tools available. Processes like milling, turning, and drilling are effective but can’t easily produce the intricate internal structures or organic shapes that additive manufacturing can. However, traditional methods excel in mass production and are highly efficient when producing large volumes of standardized parts.
It sounds like each method has its strengths. Laura, what are some of the key advantages of additive manufacturing?
One of the biggest advantages is customization. Additive manufacturing allows for the easy customization of products, which is difficult and costly with traditional methods. For instance, in healthcare, we can create patient-specific implants or prosthetics without needing expensive molds or tooling. Another major benefit is waste reduction. Since additive manufacturing only uses the material necessary to build the object, it generates far less waste than traditional subtractive methods, which is both cost-effective and environmentally friendly.
I agree, especially on the waste reduction point. Traditional manufacturing processes often result in significant byproducts, especially in metalworking. However, it’s worth noting that traditional methods are still more cost-effective for large-scale production. If you’re manufacturing millions of identical parts, traditional methods with established supply chains and economies of scale are often more efficient.
So, it’s a balance between customization and scalability. What about the equipment and facility requirements? How do they differ between these two methods?
Additive manufacturing generally requires simpler, more compact equipment. Many 3D printers are desktop-sized and can operate in relatively small workshops. However, industrial-grade additive manufacturing systems still need significant space, especially when working with metal powders that require controlled environments.
Traditional manufacturing often requires a much larger infrastructure. You need space for different machines like lathes, mills, and drill presses, each dedicated to a specific part of the process. Additionally, traditional manufacturing typically needs a more extensive setup for assembly lines and quality control, which can be resource-intensive but is necessary for high-volume production.
With these differences in mind, where do you see the future of manufacturing heading? Will one method dominate, or is there a place for both?
I believe both will coexist and complement each other. Additive manufacturing will continue to grow, particularly in industries where customization and complex designs are critical. We’ll see more hybrid approaches where parts are initially 3D printed and then finished with traditional methods to achieve the best of both worlds.
I agree. Traditional manufacturing isn’t going away anytime soon, especially in industries where mass production is key. However, as additive manufacturing technology advances and becomes more accessible, we’ll likely see it integrated more into traditional production lines, allowing manufacturers to leverage the strengths of both methods.
This has been a really insightful discussion. Thank you both for sharing your expertise. It’s clear that both additive and traditional manufacturing have unique strengths that can be leveraged depending on the specific needs of a project.
Thank you, Eric. It’s been a pleasure to discuss these exciting developments.
Likewise, Eric. It’s always great to explore how the industry is evolving.
To our listeners, thank you for joining us on Stanford Advanced Materials. If you’re interested in learning more about the materials and technologies shaping the future of manufacturing, be sure to subscribe for more insightful discussions. Until next time, keep exploring the world of advanced materials!