Chromium Carbide/Nickel Chromium Powder Description
Chromium Carbide/Nickel Chromium is a chemically clad composite powder made of nickel-chromium alloy-encased chromium carbide particles. These composite powders are ideal for thermal spray coatings, welding, HVOF operations, and other applications because they are highly wear- and corrosion-resistant in high temperature settings.
Chromium Carbide/Nickel Chromium Powder Specifications
Chemical Composition
Product
|
Chemical Composition (%)
|
C
|
Ni
|
Fe
|
Cr
|
O
|
Cr3C2-20NiCr
|
8.0-10.5
|
14.5-17.0
|
≤0.3
|
Bal.
|
≤0.5
|
Cr3C2-25NiCr
|
7.5-10.0
|
17.5-21.0
|
≤0.3
|
Bal.
|
≤0.5
|
Specification
Operating Temperature
|
≤870°C
|
Density
|
2.3 g/cm3
|
Material
|
Cr3C2/NiCr
|
Appearance
|
Dark Gray Powder
|
Average Particle Size
|
45 +5.5 µm
|
Chromium Carbide/Nickel Chromium Powder Application
- Thermal Spray Coatings: These powders are employed in thermal spray processes to create protective coatings on surfaces, such as turbine blades, exhaust systems, and industrial furnace components, to enhance their resistance to high temperatures and corrosion.
- Metal Cutting and Machining Tools: Chromium Carbide/Nickel Chromium coatings can be applied to cutting tools, drills, and milling inserts to extend their lifespan and maintain sharp cutting edges in high-stress cutting operations.
- Mining and Quarrying Equipment: Components exposed to abrasive materials in mining and quarrying machinery benefit from these coatings to reduce wear and prolong operational life.
- Aerospace and Aviation: The powder is used to coat aircraft engine components, providing protection against high-temperature environments and abrasive conditions, thereby improving engine efficiency and durability.
- Oil and Gas Industry: It finds application in downhole drilling equipment and wellbore components to withstand the abrasive nature of drilling operations and high-pressure, high-temperature environments.
- Automotive: Chromium Carbide/Nickel Chromium coatings are used in engine parts and transmission components to enhance wear resistance and reduce friction, contributing to improved fuel efficiency and longer component life.
- Power Generation: Components in power plants, such as boiler tubes and turbine blades, utilize these coatings to withstand extreme temperature variations and corrosive conditions, ensuring reliable energy production.
Chromium Carbide/Nickel Chromium Powder Safety Information
Signal Word
|
Danger
|
Hazard Statements
|
H317-H351-H372
|
Hazard Codes
|
T
|
Risk Codes
|
R40 48/23 43
|
Safety Statements
|
N/A
|
Transport Information
|
NONH for all modes of transport
|
GHS Pictograms
|
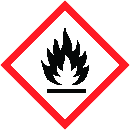
|
Chromium Carbide/Nickel Chromium Powder Packaging
25KG per drum or as required
Our Chromium Carbide-Nickel Chromium Powder is clearly tagged and labeled externally to ensure efficient identification and quality control. Great care is taken to avoid any damage which might be caused during storage or transportation.
Chromium Carbide/Nickel Chromium Powder FAQs
Q1: What is Chromium Carbide/Nickel Chromium Powder?
A1: Chromium Carbide/Nickel Chromium Powder is a composite powder consisting of chromium carbide particles embedded in a nickel-chromium matrix. This powder is used for thermal spraying and other coating processes to provide surfaces with enhanced wear and corrosion resistance.
Q2: How does Chromium Carbide/Nickel Chromium Powder compare to other coating materials?
A2: Chromium Carbide/Nickel Chromium Powder offers superior wear and corrosion resistance compared to many other coating materials. Its ability to withstand high temperatures makes it ideal for applications where other coatings might fail. The combination of hardness from chromium carbide and toughness from the nickel-chromium matrix provides a balanced performance for demanding environments.
Q3: Can Chromium Carbide/Nickel Chromium Powder be used in different thermal spraying processes?
A3: Yes, Chromium Carbide/Nickel Chromium Powder can be used in various thermal spraying processes such as plasma spraying, HVOF (High Velocity Oxygen Fuel) spraying, and flame spraying. Proper process parameters should be followed to achieve optimal coating quality.